Optimizing Air Quality & Reducing Costs in Clean Rooms with ASPRA INduct Systems (as HEPA)
Minimizing Maintenance, Downtime, and Energy Consumption in Controlled Environments
Maintaining optimal air quality in clean rooms is essential, yet the conventional use of HEPA filters presents significant challenges. These filters require multi-stage filtration and frequent maintenance, leading to high energy consumption and operational costs. Additionally, maintenance demands production stoppages and costly re-validations, impacting efficiency and profitability.
To address these issues, ASPRA Induct systems were integrated between the Air Handling Unit (AHU) and HEPA filters, significantly reducing maintenance frequency and downtime. This innovative solution offers a more efficient, cost-effective alternative, extending HEPA lifespan while ensuring ISO standard compliance.
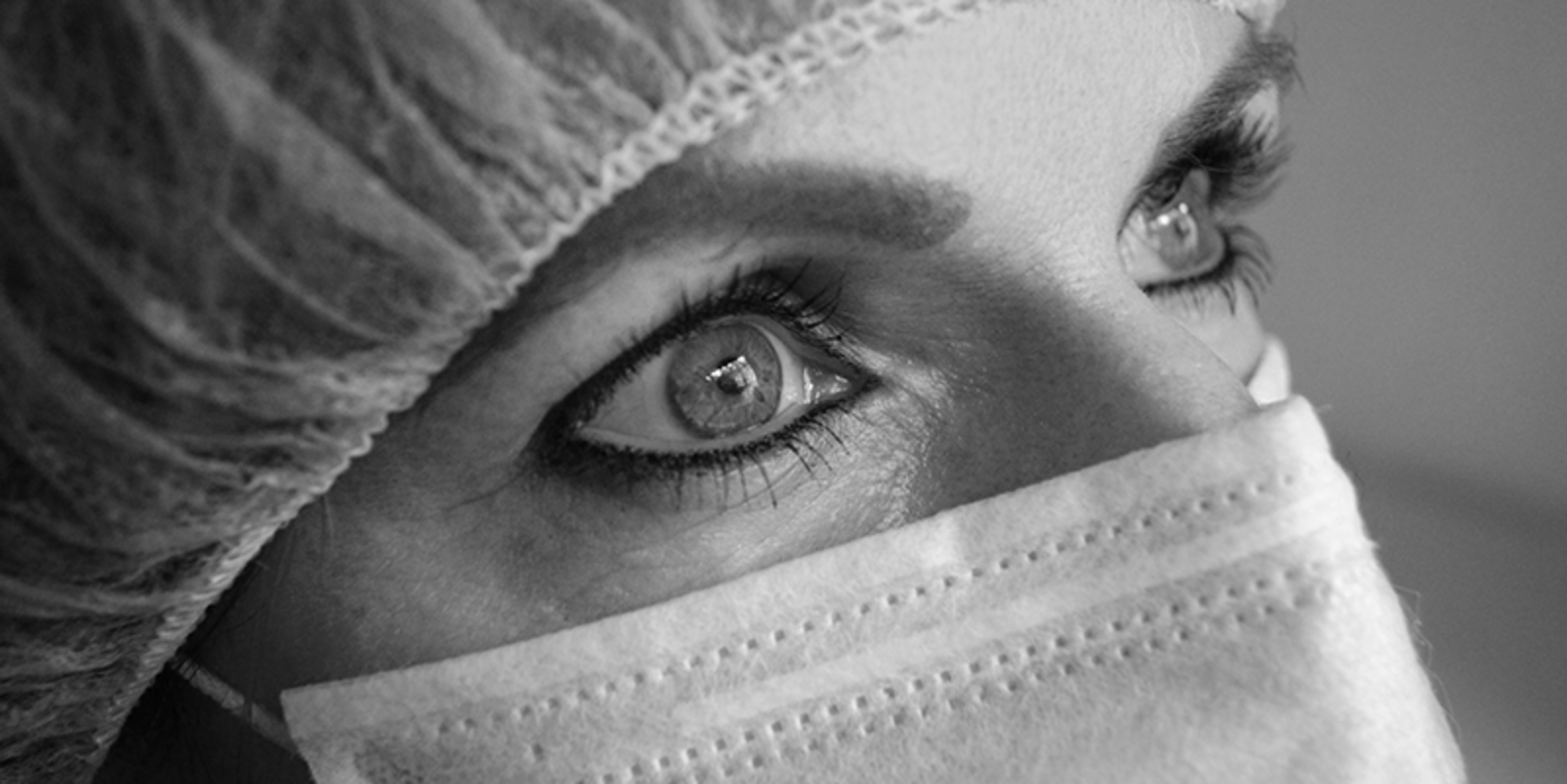
About the Project
Clean rooms rely on multi-stage filtration to maintain stringent air quality requirements, with HEPA 13 or 14 filters often installed in the plenum. However, this setup leads to high pressure drops, causing increased energy consumption and frequent, labor-intensive maintenance.
Replacing or maintaining HEPA filters in clean rooms necessitates production stoppages and re-validation, resulting in substantial costs depending on the ISO class of the facility. To combat these challenges, ASPRA Induct systems were implemented, positioned between the Air Handling Unit (AHU) and HEPA filters. This reduces the load on HEPA filters, prolonging their lifespan and lowering maintenance costs while keeping clean rooms compliant and operationally efficient.
Client
Sector
Location
Product
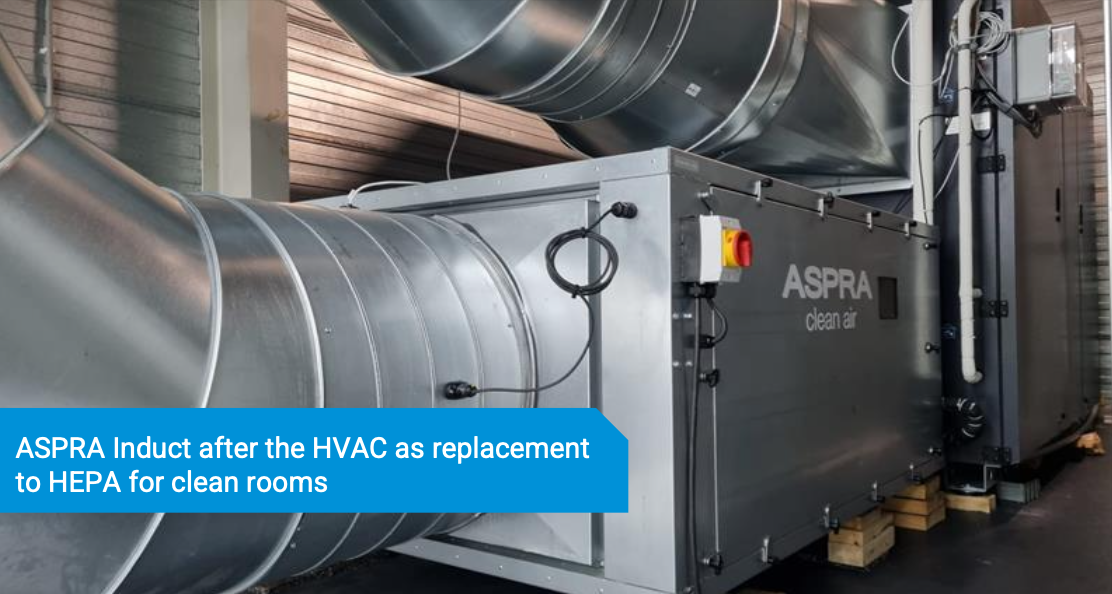
Summary
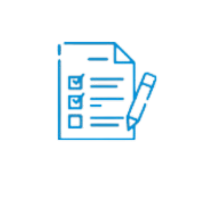
1. Problem
Operating and maintaining HEPA filters in clean rooms is expensive and labor-intensive.
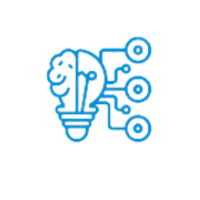
2. Solution
Implemented the ASPRA Induct system between the Air Handling Unit (AHU) and HEPA system to reduce maintenance frequency and production stoppages.
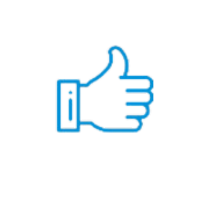
3. Result
Reduced maintenance frequency and downtime, offering a more efficient and cost-effective alternative while ensuring compliance with clean room standards.
Highlights
Reduced HEPA maintenance frequency, minimizing costly interventions.
Lower costs due to reduced production stoppages and re-validation requirements.
Energy savings achieved by reducing pressure drops in filtration.
Extended HEPA lifespan, ensuring compliance with ISO standards while optimizing cost efficiency.
Detailed Approach
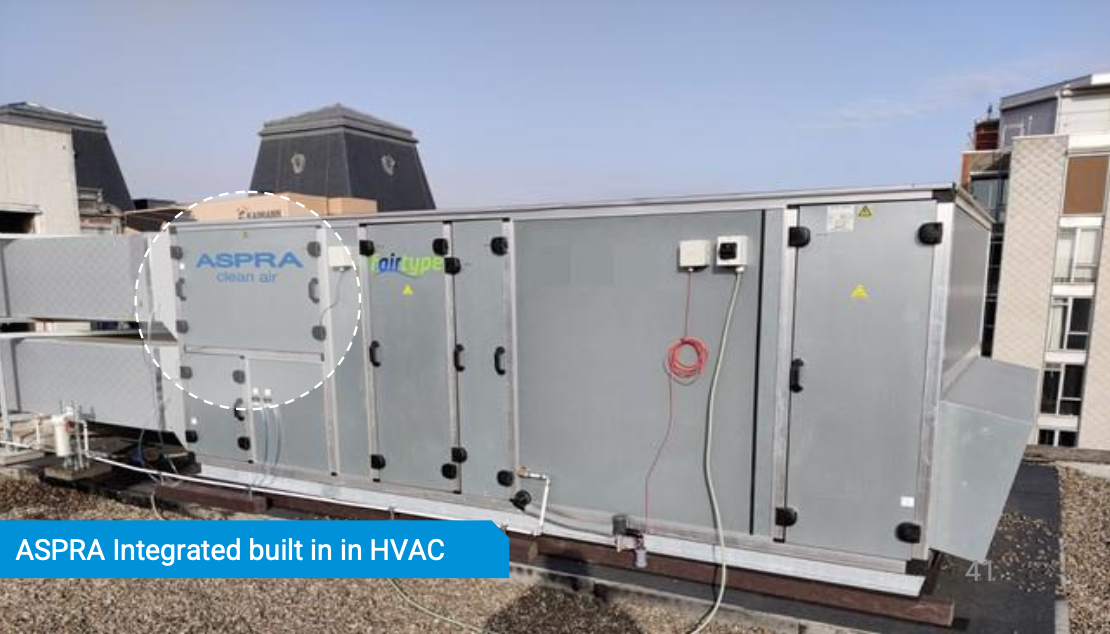
Problem Description
Clean rooms rely on multi-stage filtration, with HEPA 13 or 14 filters often installed in the plenum to remove airborne contaminants. However, these multiple filtration stages create high-pressure drops, increasing energy consumption and operational costs.
Regular HEPA filter maintenance requires shutting down production, performing system re-validations, and replacing clogged filters, all of which incur significant expenses depending on the ISO classification of the clean room.
The Solution
To minimize HEPA filter maintenance frequency and prevent unnecessary production stoppages, ASPRA Induct systems were installed between the AHU and HEPA filtration units. This pre-filtration solution captures particles before they reach the HEPA filter, ensuring a cleaner airflow while reducing HEPA workload.
By reducing particle load on HEPA filters, ASPRA technology extends filter lifespan, lowers operational costs, and maintains compliance with ISO air quality standards. Alternatively, ASPRA can be fully integrated into the AHU, eliminating the need for HEPA filters altogether.
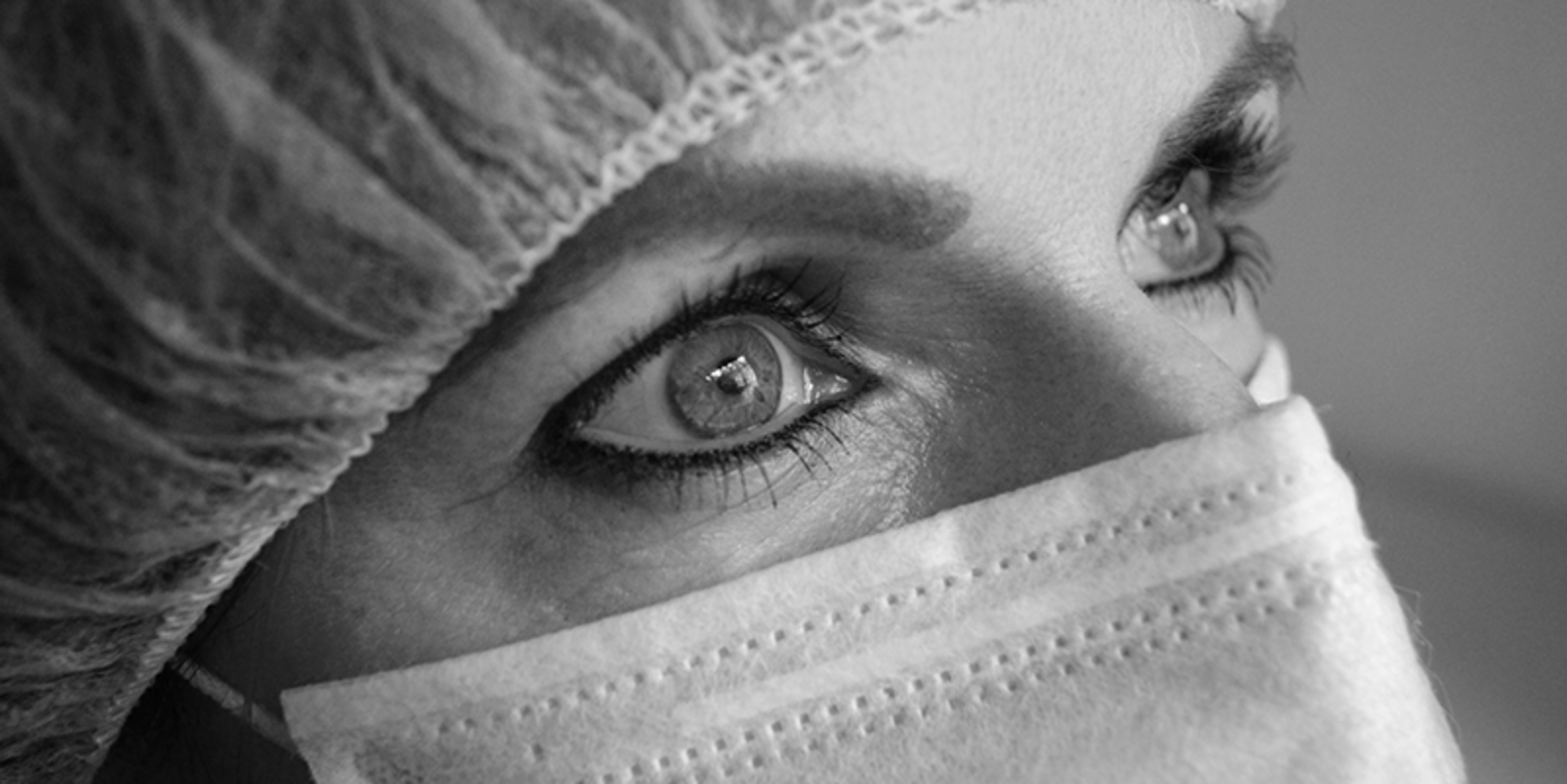
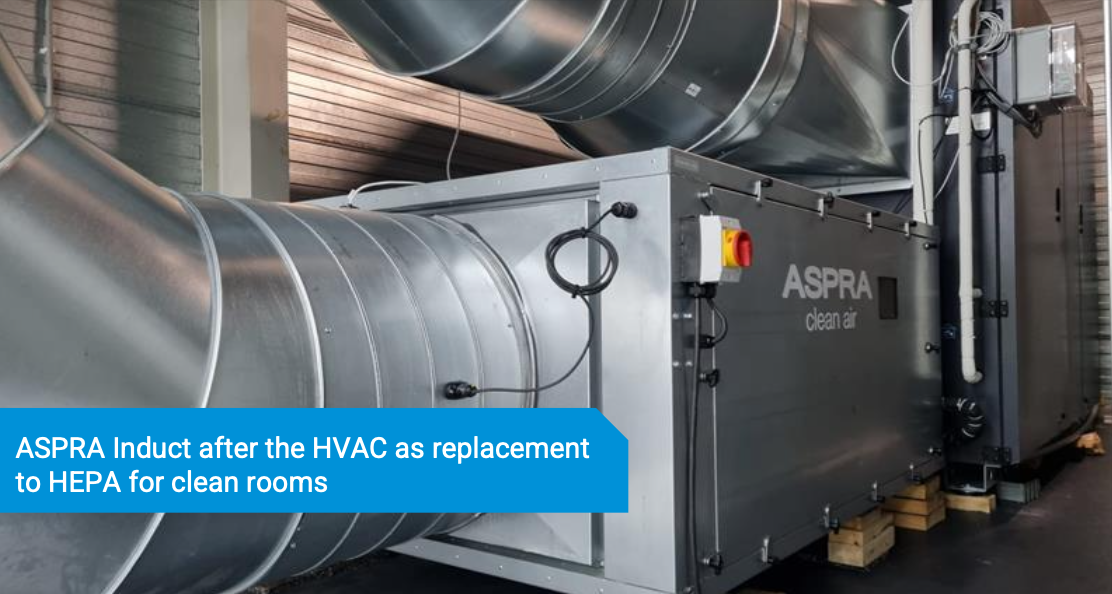
The Result
The implementation of the ASPRA Induct system resulted in major cost reductions by significantly extending HEPA filter life—allowing replacements only when required for ISO compliance.
Key benefits included:
✔ Up to 80% cost savings on HEPA filter replacements and maintenance.
✔ Reduced energy consumption due to lower pressure drops.
✔ Elimination of frequent production stoppages, improving operational efficiency.
✔ Cleaner air while maintaining full compliance with clean room standards.
More Projects in Healthcare & Clean Rooms
Contact & Services
Contact our experts for tailor-made advice: